In 2011 Trotec presented DirectMark, the first print driver using a printing function from any software for direct part marking with a galvo laser system. And now our recent release features many new fun and exciting features!
Organizing Your Printing Jobs:
Optimizing the features of our first release, managing print jobs will now be easier than ever!
Job Time: In order to facilitate job time estimation and productivity the marking time is now displayed for each job!
Job History: Provides a comprehensive overview of how many copies were marked, a what time, and how long each mark too.
Archive: Now you can save spool files, so when additional copies are needed after completing production you can reload the directly instead of having to print them again from your graphic software.
Password Protection: Never lose your optimized settings again... With a password protection your unique settings are just a click away!
New Hardware Options:
Added features increase the productivity and versatility of your laser!
Rotary: The new DirectMark 1.2 release is compatible with Trotec's rotary unit... Allowing you to mark cylindrical parts; like rings, cups, tools, and much more!
Foot Switch: Makes marking multiple jobs quick and easy, just tap the foot switch to trigger the next mark!
To the operator the DirectMark driver appears as a standard properties dialogue linked to the print function and a printer queue to handle pending jobs.
This was made possible by a team of software developers and laser engineers putting years of experience into Trotec's driver in order to offer features like the material database... Which makes picking the right laser parameters as easy as selecting the material of your choice from a list or the Logo Mode, which automatically vectorizes any graphic before sending it to the laser, making good use of our high speed scan heads.
DirectMark print driver is standard on the ProMarker and available as an option on all SpeedMarker FL Marking Systems.
What are your thoughts? How will (or have) these features help on your production line? What would you like to see on our next release? Looking to keep up-to-date with Trotec? Check out more articles, trade show information, and more under "News" on our website!
There are many misconceptions about safety requirements of laser operation as well as many factors being left unknown to even the most seasoned laser operator. Everyone at Trotec is dedicated to educating our customers on their machine and how to safely operate it at all times.
With this in mind I would like to go over a few of the basics with you; including laser classification, proper handling of laser components, and general rules of safe operation.
Laser Classification
There are 5 different classifications of a laser. The classification rating is based on the capability and/or possibility of the laser injuring an operator during use. Injury can include burns to the cornea, severe burns to skin, and danger of fire to clothing and other objects. The classifications are denoted mostly by roman numerals and sometimes letters (i.e. III, III-A).
Trotec’s flatbed laser systems fall under the Class II Laser Safety requirements, meaning that one is exposed to invisible laser radiation but is protected due to the machine’s safety precautions; including: protective lid (has a protective coating to disperse radiation levels), interlock system (prevents the laser from operating if lid or side panels are opened or not properly in place), and ability to stop laser process instantly.
Unless installed in a work station, Trotec’s Galvo laser systems fall under the Class IV Laser Safety requirements, meaning one is directly exposed to invisible radiation and there are not any safety precautions installed. Lasers can cause severe and permanent damage to your eyes if not protected. When operating a Class IV laser it is imperative to where regulated protective glasses to protect your eyes from invisible radiation. There are laser safety goggles available that will protect your eyes from the radiation, for more information on purchasing the correct safety goggles please contact our Technical Support Team. Safety guidelines are regulated by both OSHA and local authorities, so when operating a Class IV laser it is important to check your local guidelines.
Proper Handling of Laser Components
Lenses: It is important to check your lens on a regular basis. If the lens is dirty you will want to clean it, proper lens cleaning is discussed in Clean Lens Clean Results.
The chemicals used to make laser optics are hazardous, so never handle the bare, cracked, or broken lenses without protective gloves. It is important to dispose of used laser optics at a licensed industrial waste facility, which is in compliance with all local, state, and federal regulations. Check local listings for a facility near you. If you do not have a local waste facility, you may return the lens in a sealed zip-lock bag to Trotec for proper disposal.
For more information on proper cleaning and maintenance of your laser please refer to our blog, Better Health for Your Trotec.
Safe Operation
It is important to understand safe operations of the laser. There are a few simple rules to follow to ensure your laser machine remains in working condition.
To start, never leave a laser unattended while running a job. The laser is burning through materials and if left unattended the materials could catch fire and burn within your laser system. This can severely damage your machine, your place of business, and anyone located within the building.
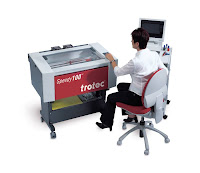
Continuing with the possibility of fire and potential damages, always run your laser with a proper fume extraction system. It is easy to setup proper fume extraction either internally or externally. If you choose to exhaust externally always check the specific requirements such as CFM before purchasing a system.
Trotec offers easy to use internal filtration systems that can be programmed to turn on when the laser is processing jobs and turn off after completion. If you already use one of Trotec’s fume extractors, always remember to replace your filters when the machine indicates to do so.
Proper wiring and electrical requirements for the laser at your facility are critical. Most of our systems run on 115V with 15 Amps; however, many of our large format and higher powered systems required 220V with 20 Amps.
Trotec offers free phone technical support throughout the life of your laser, if you have any questions about preparing your facility or safety requirements please do not hesitate to contact us.
Meet the Author of "Laser Safety": Josh Stephens
Back to You: Do you have any more questions about laser safety. Let us know, we're happy to help!
Everyone at Trotec Laser, Inc. would like to wish
you and yours a Happy New Year! We hope every goal and aspiration you have set
come to fruition in 2012!
On behalf of all of us here at Trotec, I
would like to extend our gratitude for the wonderful year we had in 2011! It has been a pleasure helping you reach your goals. We are very grateful for good customers like you, who make our work satisfying and enjoyable. We look forward to working with you in 2012 and contributing to your success!
We have very many exciting developments on the horizon! First on the agenda is ARA 2012! We all hope to see you in Las Vegas this March, as we plan to kick off the trade show season with a BANG! If you cannot make it out to ARA we have many more shows throughout the country this year, many of which we are offering free passes to attendees... So there is sure to be a show in your neck of the woods.
We recently got some very exciting news... Trotec's Speedy 300 Flexx was selected to receive CorelDrawHelp Magazine's 18th Annual Top Product of the Year Award (see page 20), recognizing the the versatility, speed, durability, and uniqueness of the Flexx!
Once again, thank you for a great 2011 and we look forward to working with everyone in 2012 (and for many years to come)!
Happy New Year!
Over to You! What are you excited about for 2012? Are you planning on attending any trade shows this year?